How Regional Distributors Can Improve Middle Mile Logistics
May 2, 2024
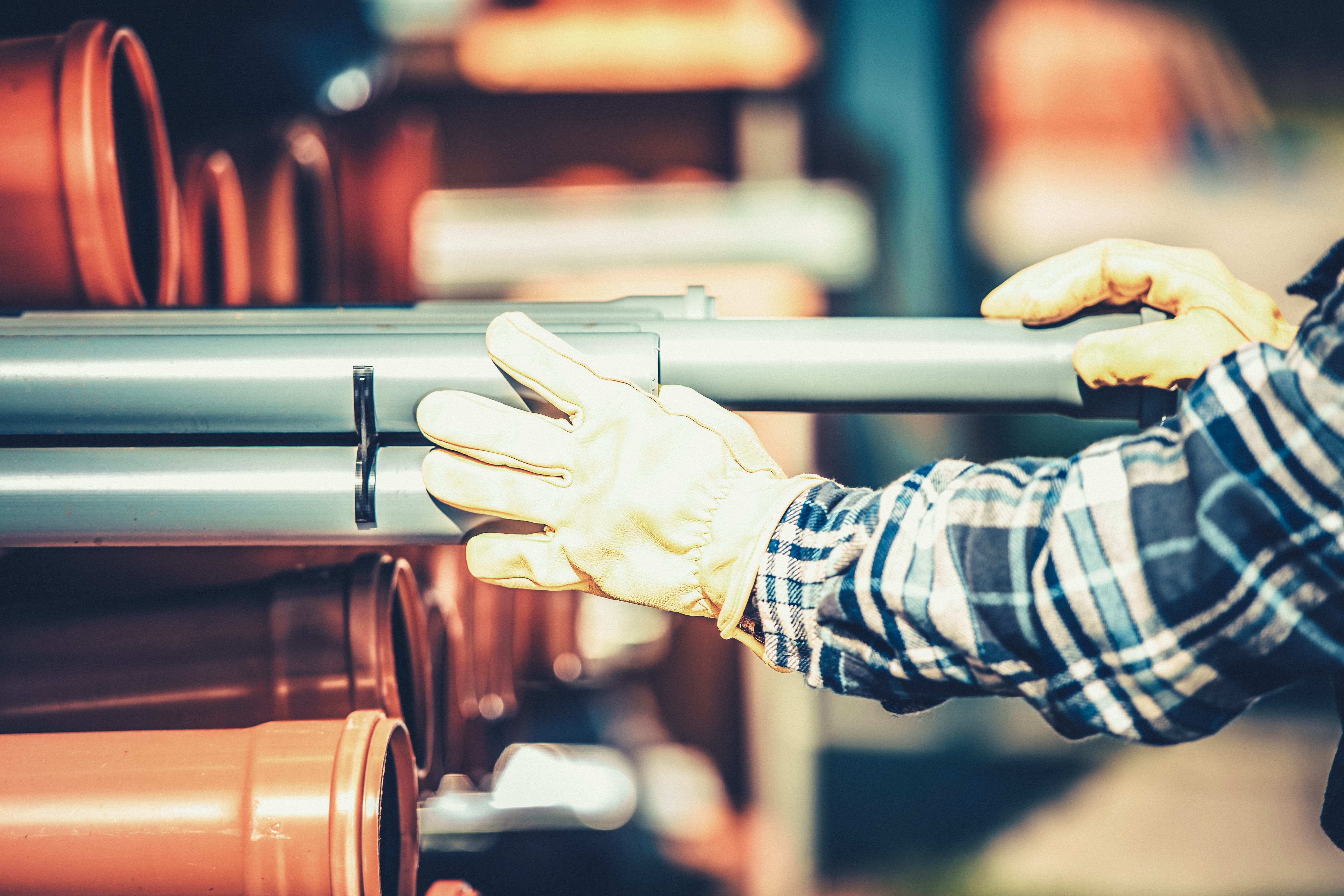
The construction industry has dealt with multiple challenges recently, and some persist. The supply chain is one of those issues. Although supply chain issues have eased somewhat, they continue to be a factor the industry needs to deal with. Snags have occurred at each of the delivery points, including the middle mile. If materials are not moving in a timely manner from the regional distribution level, retailers, big box outlets, etc., will not be able to get the product to the consumer.
This is where middle mile logistics comes into play. In this article, we’ll explore the importance of middle mile logistics and show ways you can improve it.
Understanding middle mile logistics
What Is middle mile logistics?
Middle mile logistics is the center of the delivery process and connects the first mile and last mile. During this delivery phase, goods and materials are transported from regional distribution centers to retail outlets or other facilities that will lead to the final customer.
This phase of the logistics sequence is often overlooked since end customers don’t deal with it directly. Despite this, the logistics involved with this delivery phase are complex and impactful. If goods and materials are not transferred to their next destination in the supply chain, end customers will be affected.
Using technology like route planning and tracking trucks in real time helps make this process better by avoiding delays and reducing the time goods spend in transit.
First mile vs middle mile
The journey begins in the first mile, where products are collected from their manufacturing sites. This stage is pivotal as it sets the pace for the supply chain's efficiency. Goods are transported from their origin to the nearest warehouse or distribution center.
Following the first mile, the middle mile logistics takes over by moving these goods from the primary warehouses to secondary distribution centers. This leg of the journey is often longer. It involves significant logistical planning to ensure cost-effectiveness and timely delivery.
Unlike the first mile, the middle mile requires handling larger volumes and coordinating multiple transportation modes, making it a bridge between the production side and the consumer-facing last mile.
Middle mile logistics vs last mile
After goods are gathered from their manufacturing origins and processed through the first mile, they enter the middle mile phase. This involves moving the products from primary warehouses to secondary distribution centers or directly to retail outlets. It's a critical step that requires handling large volumes and coordinating various modes of transportation.
In contrast, last-mile logistics is the final step in the delivery process, involving the delivery of goods to the end consumer.
Thank you for reading this article. Please enjoy $40 off any Curri delivery by clicking on this link to sign-up.
Importance of middle mile logistics for regional distributors
The efficiency of middle mile logistics is crucial for regional distributors.. Here are three key ways it impacts their operations:
Streamlining supply chain efficiency
Middle mile logistics is pivotal in streamlining the supply chain. Efficient middle mile operations ensure that goods move smoothly from primary distribution centers to secondary locations, which helps maintain a continuous supply chain flow. This reduces downtime and increases the overall efficiency of the supply chain. This allows regional distributors to meet customer demands promptly and effectively.
Reducing operational costs
Cost reduction is a significant benefit of optimized middle mile logistics. By improving route planning and load optimization, distributors can lower transportation costs. Efficient middle mile logistics also minimizes the need for excess inventory at distribution centers, reducing storage costs and lessening the risk of inventory depreciation.
Enhancing customer satisfaction
Timely delivery is important for maintaining customer satisfaction. An effective middle mile logistics strategy makes sure that products are available when and where they are needed.This is vital for meeting the quick turnaround times demanded by retailers and end consumers. Improved reliability and efficiency in the middle mile can lead to increased trust and loyalty from customers, as they receive their orders on time and in good condition.
Key challenges in middle mile logistics
The middle mile is like the baton between the other two stages of the delivery process. Without it, the supply chain can’t function.Goods and services that are coming into the regional distribution center are sent to multiple locations to ensure each retail outlet has its needed supply. The longer supplies remain at the regional distribution center, the more time the final customer waits. So, trucks need to stay on schedule.
Bottlenecks in distribution centers
Bottlenecks at regional distribution centers represent a significant challenge in middle mile logistics. They occur when there's an overload of incoming shipments that exceeds the processing capacity of the facility. This leads to delays in sorting, storing, and forwarding goods to their next destinations. This inefficiency can be made worse by inadequate facility layout, limited storage space, or insufficient staffing levels.
Inefficiencies in route and load management
Another challenge is ensuring each retail outlet gets its correct shipment. Last-minute changes can be particularly challenging and complicate logistics. Without optimal route planning and vehicle loading strategies, vehicles may travel with partial loads or take longer routes than necessary, wasting fuel and time. Advanced routing algorithms and real-time GPS tracking can help by making sure that vehicles are fully utilized and travel the shortest possible routes to their destinations.
Fluctuating demand and supply chain disruptions
Adapting to fluctuating demand and unexpected supply chain disruptions poses another challenge. Demand can vary due to seasonal trends, market fluctuations, or unforeseen events, requiring distributors to adjust their logistics strategies rapidly. Flexibility in the logistics network, robust inventory management, and effective communication among all stakeholders are crucial to responding swiftly to changing conditions.
Addressing all of these challenges requires a combination of technology, strategic planning, and proactive management. By focusing on these areas, distributors can enhance the efficiency of their middle mile logistics, reduce costs, and improve overall supply chain resilience.
How to improve middle mile logistics?
Curri offers companies a solution to their middle mile logistics challenges. Our flexible and reliable delivery service helps companies make sure goods are delivered as scheduled. The service is available as needed, and companies only pay for delivery when they use it. We have vehicles of all sizes available, so companies can work with Curri on any delivery, making logistics headaches disappear. They can do their part to minimize the supply chain challenges that have hit the industry.
Reduce costs from in-house delivery fleets
Every vehicle that is part of the fleet is an added expense. There’s maintenance, upkeep, insurance, etc. It doesn’t matter if the vehicle is in use all day, every business day, or periodically. However, minimizing the fleet means a reduction in fixed costs.
Determining the correct number of delivery vehicles so you're always prepared to make the trip from your regional distribution center to the next step in the supply chain is nearly impossible. So, most companies will have extra – just in case. Again, that adds to fixed costs and reduces the bottom line.
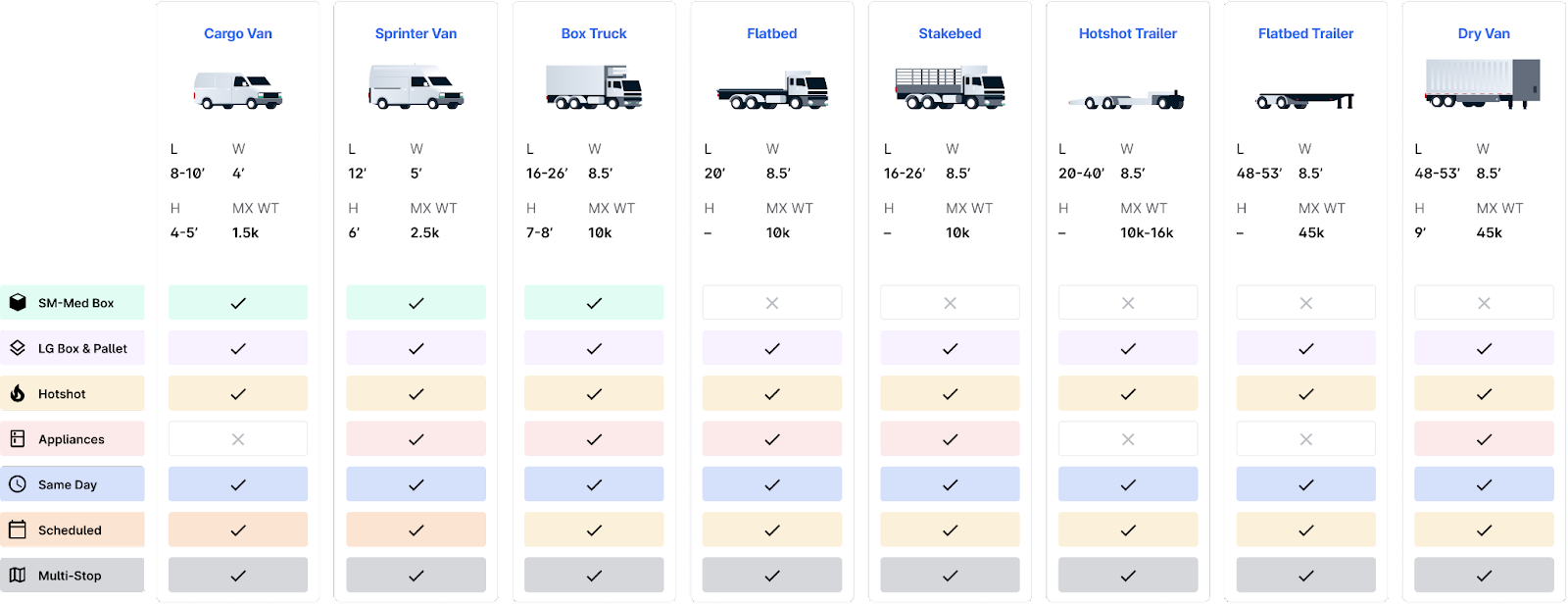
Adding Curri to your team allows you to reduce or eliminate your fleet and not lose reliability and dependability. The only loss is fixed costs since you only pay for what you need.
Thank you for reading this article. Please enjoy $40 off any Curri delivery by clicking on this link to sign-up.
Provide on-demand same-day transportation
Some days, you need an extra hand. Maybe, a shipment went out and was missing some industrial gear that a retailer needs desperately. Perhaps supplies of equipment have been out and finally came in. Your retail outlets can’t get enough of it, so distribution needs are through the roof.
With Curri’s industrial-grade hotshot deliveries, you can make one-off deliveries. Book vehicles easily and quickly, and rest assured that your orders will be delivered safely, on time, and accurately. Get the extra hand you need and keep the retail chains stocked.
Make exception management quicker and easier
Is stability too much to ask for? If every day was the same, management would have a much easier time handling logistics. It's the exceptions that cause management to pull their hair out as they try to find solutions.
Our platform manages delays, unexpected site conditions, and changes in materials availability to help you stay on schedule and within budget. It makes exceptions easier to handle for management. At Curri, we know exceptions are the norm, and our solution helps you make the hard decision more easily and quickly.
Addressing driver shortages and staffing challenges
The United States has had a shortage of truck drivers for years. It grew in the mid-2010s and has stayed at an elevated level. So, hiring and retaining qualified employees is a challenge all employers face. A distribution center can’t function without drivers. Both insufficient staff and someone out for a limited time impacts delivery time.
You can partner with Curri to bridge long-term gaps in staffing. Our on-demand dedicated routes offer you the convenience of a dedicated driver and vehicle tailored to your requirements, available for a minimum of one day. This service is available while a long-term solution is determined. Whether it’s a local run or a long haul, we have staff available, so your distribution happens as needed.
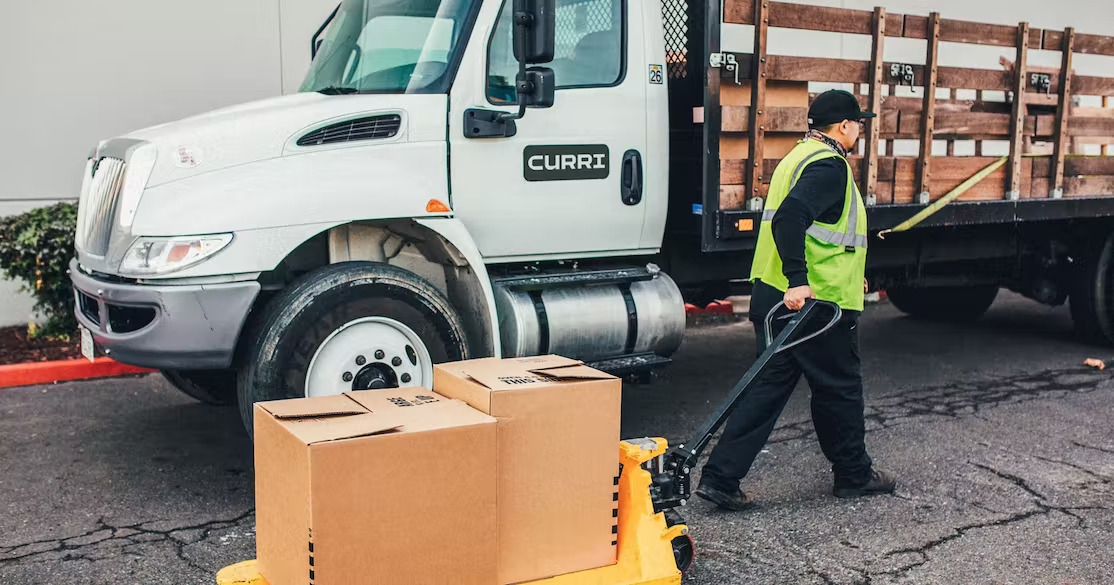
Curri's model allows for quick scaling of driver resources, ensuring that deliveries can be made without interruption. This approach not only helps cover immediate needs but also supports long-term strategic planning for staffing within the logistics sector.
Improving crisis management and response times
In the fast-paced world of logistics, the ability to manage crisis effectively is more important than ever. Curri’s logistics platform can enhance a company's crisis management capabilities by providing scalable solutions that adapt to changing conditions. Whether it's a sudden spike in demand or disruptions due to external factors, Curri can provide the necessary logistics support to handle crises efficiently, minimizing downtime and keeping the supply chain moving.
Streamlining operations for Coburn's regional distribution
Coburn’s, a distributor in the construction and building materials industry, faced significant challenges with their delivery operations.This included high costs associated with maintaining their own fleet and the inability to meet urgent delivery demands.
They used Curri Dedicated and Curri Hotshots to address these issues. This approach allowed Coburn's to reduce reliance on their own fleet, saving significant costs associated with vehicle maintenance and insurance. Curri's flexible delivery options also provided the capability to handle rush orders effectively, making sure that Coburn’s could meet their customers' needs without delay.
The impact of partnering with Curri was profound: Coburn's realized an annual savings of $150,000 and enhanced their service delivery. This case illustrates the tangible benefits of integrating Curri’s logistics solutions at the middle mile.
Take Curri’s logistics platform for a test drive
It's clear that optimizing middle mile logistics is important for enhancing operational efficiency, reducing costs, and improving customer satisfaction. We dove into the challenges distributors face, such as bottlenecks in distribution centers, inefficiencies in route and load management, and meeting fluctuating demands. Solutions like flexible fleet management, advanced routing technologies, and on-demand delivery capabilities, can address these challenges effectively. To learn more about how you can use Curri for improved middle mile logistics, book a demo or create a free account.
FAQ about middle mile logistics
How does middle mile logistics impact customer satisfaction?
While middle mile logistics doesn't involve direct interaction with the end customer, its efficiency directly impacts delivery speed and reliability. These are important for maintaining high customer satisfaction levels. Efficient middle mile operations makes sure that products are available when and where needed.
Can middle mile logistics be environmentally friendly?
Yes, middle mile logistics can incorporate sustainable practices. Using right sized vehicles and optimizing delivery routes to reduce fuel consumption are great ways to start. Managing loads efficiently minimizes the number of trips required. These practices reduce carbon footprint and also give cost savings.
How does Curri manage the reliability of middle mile delivery services?
Curri maintains high reliability by using a diverse fleet that can cater to various delivery needs. We conduct rigorous driver vetting to make sure they’re experienced. Every delivery is also backed with $250,000 of coverage. This approach makes sure that goods are delivered on time and in good condition, regardless of the complexity or scale of the delivery task.
Thank you for reading this article. Please enjoy $40 off any Curri delivery by clicking on this link to sign-up.